Overview
- Limits of the State of the Art
- Kinematic Extension of Classical Shell Elements
- Numerical Efficiency: Artificial Stiffening Effects (Locking)
Project description
Limits of the State of the Art
In order to obtain the most precise prediction possible from finite element models, both the structural modelling and the detailed description of the material using material models are of great importance. For certain applications, shell elements reach their limits of applicability. The reason for this is that in certain sheet metal forming processes the assumptions made in classical shell formulations, such as neglecting stresses in thickness direction and in particular the fact that cross-sectional fibers remain straight, no longer apply. Typical cases where these assumptions can become critical are the forming of thick sheets or bending over small radii. Here, it is not the absolute sheet thickness that is decisive, but the relationship between the sheet thickness and the component geometry. Thin sheets (e.g. with a sheet thickness of 1 mm) can therefore be critical with correspondingly small radii. There are also a number of forming processes and subsequent operations such as ironing, roll forming, folding or flanging, which cannot be adequately simulated with standard shell elements. The use of volume elements (solid elements) only offers an alternative in individual cases, since a very fine discretization in all three spatial dimensions is required.
For extended shell formulations, the simplified assumption of vanishing transverse normal stresses is dropped. Therefore, in contrast to standard shell elements, these formulations require a 3d material model that takes into account all stress and strain components. With regard to the anisotropy of the material occurring in sheet metal, in this case the sheet material has to be characterized both in the sheet plane and in the sheet thickness direction in order to determine the required parameters of the 3d material models. This is a great difficulty for the classical material characterization, since experimental investigations outside the sheet plane are very difficult or cannot be realized with sufficient accuracy. Within the scope of this project, the concept of virtual testing was further developed at Fraunhofer IWM and applied to the characterization of sheet materials outside the sheet plane.
Kinematic Extension of Classical Shell Elements
One focus of the work at our institute in this research project is the further development of shell formulations especially for the requirements of sheet metal forming simulations. By suitable extensions of the shell kinematics, these elements are enabled to more accurately represent critical forming processes. The figure below visualizes the deformation possibilities of the newly developed element. On the left side of the figure, the geometry description of a 7-parameter shell is shown. The grey area represents the shell’s mid-surface, the other lines visualize cross-sectional fibres and the thickness of the shell. The newly developed shell is additionally able to show a square warping of the cross-sectional fibres (in the middle of the figure) as well as a cubic warping (right side) and any combination of these.
In order to compare the simulated cross-sectional warping with experimental data, a draw bead test was carried out as part of the project. To investigate the warping of the sheet in the direction of the sheet thickness, small holes were made in the samples. After the draw bead test, the samples were metallographically examined to visualize the warping of the cross-sectional fibres. The figure below shows an example of the development of the cross-sectional curvature determined in the test, compared to a simulation with solid elements and the newly developed shell element. Both the solids and the newly developed shell element show a qualitatively similar cross-sectional warpage in the test. When using standard shell elements, as they are used today in the industrial context for sheet metal forming simulations, this warping could not be reproduced.
Numerical Efficiency: Artificial Stiffening Effects (Locking)
Besides the kinematic extension, the focus is on the numerical efficiency of the elements to be developed, so that they are suitable for forming simulations in industrial practice. This includes the elimination of existing as well as the avoidance of new artificial stiffening effects.
Project data
Publications
- Schilling, M., Willmann, T., Wessel, A., Butz, A., & Bischoff, M. (2023). Higher-Order 3D-Shell Elements and Anisotropic 3D Yield Functions for Improved Sheet Metal Forming Simulations: Part I. 14th European LS-DYNA Conference 2023, Baden-Baden, Germany.
- Wessel, A., Butz, A., Schilling, M., Willmann, T., & Bischoff, M. (2023). Verbesserte Blechumformsimulation durch 3D-Werkstoffmodelle und erweiterte Schalenformulierungen - Teil 2. In EFB-Forschungsberichte (Vol. 607). Europäische Forschungsgesellschaft für Blechverarbeitung e.V., Hannover. https://www.efb.de/efb-forschungsbericht-nr-607.html
- Wessel, A., Willmann, T., Butz, A., & Bischoff, M. (2022). Blechumformprozesse genauer simulieren. stahl + eisen, 2022(1–2), 44--47.
- Willmann, T., Bieber, S., & Bischoff, M. (2022). Investigation and elimination of nonlinear Poisson stiffening in 3d and solid shell finite elements. International Journal for Numerical Methods in Engineering. https://doi.org/10.1002/nme.7119
- Willmann, T., Wessel, A., Beier, T., Butz, A., & Bischoff, M. (2021). Cross-Sectional Warping in Sheet Metal Forming Simulations. 13th European LS-DYNA Conference 2021, Ulm, Germany.
- Butz, A., Wessel, A., Bischoff, M., & Willmann, T. (2020). Verbesserte Blechumformsimulation durch 3D-Werkstoffmodelle und erweiterte Schalenformulierungen. Europäische Forschungsgesellschaft für Blechverarbeitung e.V. (EFB).
- Willmann, T., & Bischoff, M. (2019). Shell Models with Enhanced Kinematics for Finite Elements in Sheet Metal Forming Simulations. 12th European LS-DYNA Conference 2019, Koblenz, Germany.
Researcher:
Tobias Willmann
- Further information
- former member
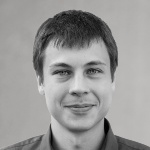
Maximilian Schilling
M. Sc.Scientific Staff